Vacuum Dehydration
Water in oil is considered a very harmful contaminant and must be recognised and managed effectively. Ignoring water contamination can lead to internal system corrosion, valve locking, parts wear, silting of orifices and valves, oil oxidation, additive depletion, pump failures and a serious effect on the oils viscosity.
What is a Vacuum Dehydrator?
A vacuum dehydrator is a water removal machine, designed to be attached to an offline system, IBC or barrel to remove all free & emulsified & dissolved water to as low as 20ppm and below.
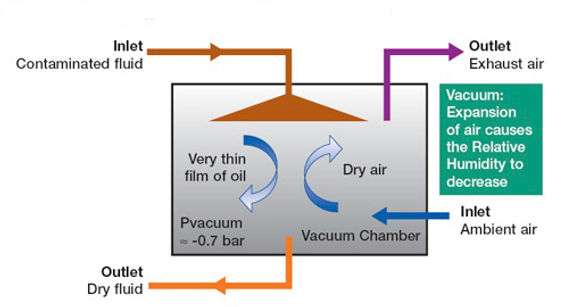
Types of Water Contamination
There are three types of water contamination in a typical system: free water, emulsified water and dissolved water.
The water saturation point of oils will vary depending on the oil type (saturation point is that point above which water is in a free form) and it is usually 200-400ppm for standard hydraulic oils, depending on age and condition. Saturation point is higher with higher temperatures.
As a guide using 100ppm for an upper water limit for most systems using oils, this means all free, emulsified and a significant portion of dissolved water must be removed. This will ensure no internal damage will be unnecessarily caused by the presence of water.
A vacuum dehydrator is one of the very successful methods to remove large amounts of water above 200ppm from oil. It will also de-gas the oils making it suitable for use on transformer oils and other oils with entrapped gases.
Free water is separate from the oil in the system and can be visually identified in a sample bottle from the oil. The specific gravity of most oils is less than 1.00, so water usually collects at the bottom of the sample bottle of reservoir/system.
For this reason, free water can easily be decanted, or removed by draining through a reservoir drain port. Decanting is recognised as a smart step, if possible, let the fluid stand or settle. This will allow the water to naturally 'split' from the oil allowing it to be drained off. Then apply the use of the vacuum dehydrator to increase the water removal speed.
Water Removal Example
The following example stated below, demonstrate the removal of water contamination from (Castrol VG32) oil by a FA-ST Vacuum Dehydrator.
The image shows the starting point of 7.5% water contamination (75,000ppm) to finish point of <50ppm (from left to right).
-
Oil: Hydraulic 32 visc oil
-
Volume: 1,400 litres
-
Start Point: 7.5% water (75,000ppm)
-
Finish point: <50ppm
-
Water removed: 105 litres

How does it work?
The vacuum dehydrator heats the oil (approx 60°C) and draws a vacuum (18-27"Hg) on the oil. Raising the temperature, whilst drawing a vacuum causes water to change to steam at a temperature low enough not to cause thermal breakdown of the oil. At sea level, water changes to stream 100°C (boiling point of water). The target zone draw a higher vacuum to change the 'state' of water to steam at a lower temperature, (keeping in mind a higher vacuum is faster water removal than lower vacuum, so we balance between low temperature and water removal rate, this creates an economical process.)
The dehydrator works on oils from mineral base to synthetic, gear oils with high viscosity and transformer oils. It's guaranteed to remove the unwanted water in your system to a target of <100ppm and further is needed.
There are other ways to remove free water from the system, such as water-absorbing filter elements which we also use and coalesce technology on limited oils without aggressive additive packages. However, to possess the capability to remove water from every oil regardless of additive package or oil type or viscosity, the vacuum dehydrator is the most cost effective on large volumes of oil. After dehydration our water absorbing elements are used to give the oil a final polish and to remove particulates to ensure the oil is clean and dry. All this is backed up by Laboratory analysis, so you can ensure that the process has worked successfully.
We welcome enquiries and can accept customer's oil at our premises for water removal and filtration to exceptional cleanliness levels. The dehydrator unit will process 1200 litre per hour and can economically viable remove up to 70% water saturation. To date most of the oils that we have cleaned have shown from 0.5% to 8% water content.

The FA-ST dehydrator runs on 415v 3 phase supply, it was designed and purpose built to fit inside our service van so that it could be taken to customers sites if required. Due to the technical nature of this unit it is only available to hire with our operator. For long term hire we can offer training for self-operation.